Challenges
Without a durable, reliable, and efficient packaging assembly, the semiconductor is susceptible to corrosion, heat, moisture, and physical impact as well as weakened connections to external circuits. Therefore, it is necessary to create a good cover and assists to protect the die and the wire bonding while also passing the most stringent moisture and temperature tests.
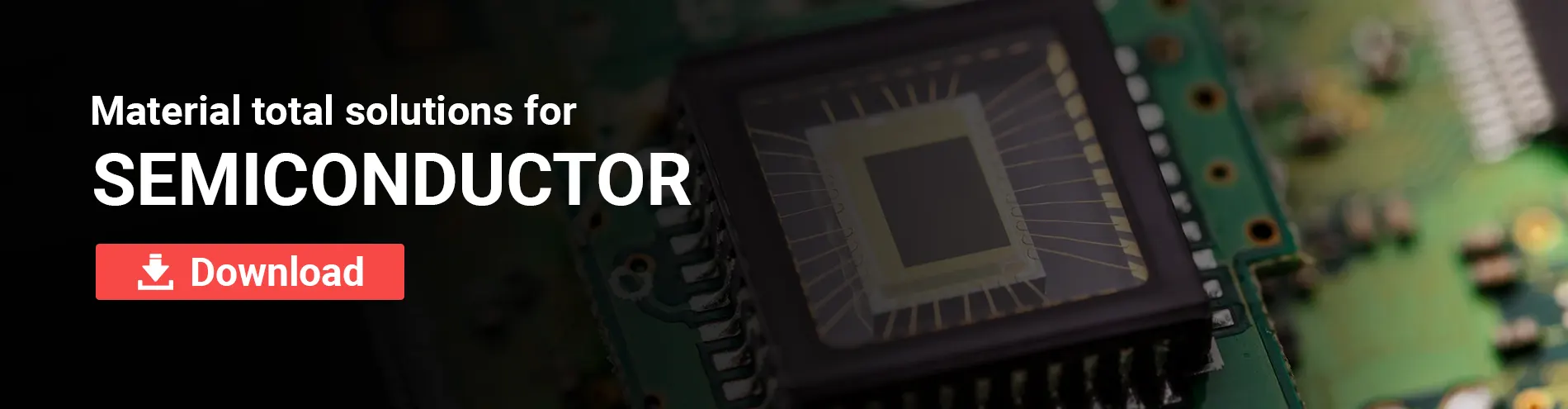
Solutions
Liquid encapsulants
Encapsulants are the last piece of the IC package and serve to protect the conductor and wires from environmental and physical damage. Encapsulant materials come in three basic varieties. The primary material is epoxy, either pure or blended. Epoxies consist of organic resins and are generally affordable, hence their popularity among manufacturers. Another widespread material used in encapsulant IC chips is silicone, which is not carbon-based and therefore not an organic resin. Silicone resins are generally solvent-based. Alternately, some resins are room-temperature vulcanizable, and contact with moisture can cure them. Silicones are popular due to their flexibility in hot as well as cold settings.
Features:
- Single dispensing system
- Flexible projects with lower throughput
- Small investment
- More expensive
- Lower cure temperatures
- Can achieve flatter and thinner packages
- Leads miniaturization
- No wire sweep
Epoxy molding compound
Epoxy Molding Compounds (EMC) by their nature have very good electrical insulation properties. Epoxy Mold Compounds are often called “functional epoxies” or “high solid epoxies” because they are heavily loaded with fillers.
These fillers, (typically silica, though other fillers are used for other properties such as thermal conductivity) are loaded more than 50% by weight be default. Highly filled systems have weight % filler loadings higher than 70% with “very highly filled loadings” as high as 92% filled by weight.
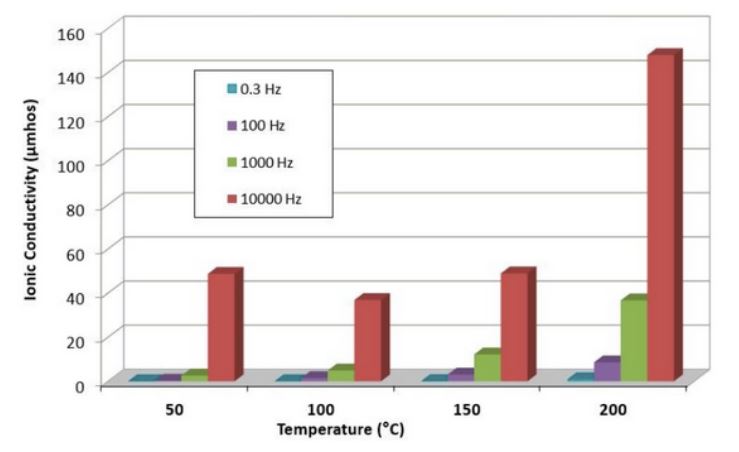
FAQs for Epoxy Molding Compound
These highly-filled systems provide epoxy molding compounds with very good dielectric strength and a very high breakdown voltage, which themselves are good electrical insulation properties. These two values, however, are poor indicators of what is meant by “Good electrical stability” for EMCs.
Features:
- Custom molding machines and plates
- Fixed projects with higher throughputs
- Large investment
- Cheaper volume for volume
- Higher cure temperatures
- Packages are relatively thicker
- Larger packages
- Can cause wire sweep
For more information, contact our specialists:
Without a durable, reliable, and efficient packaging assembly, the semiconductor is susceptible to corrosion, heat, moisture, and physical impact as well as weakened connections to external circuits. Therefore, it is necessary to create a good cover and assists to protect the die and the wire bonding while also passing the most stringent moisture and temperature tests.
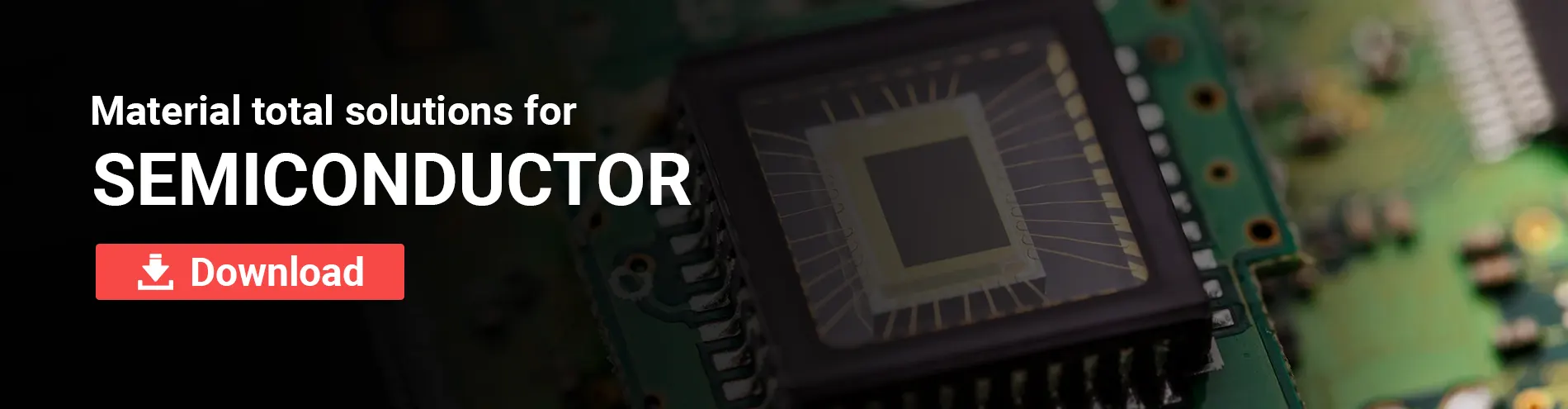
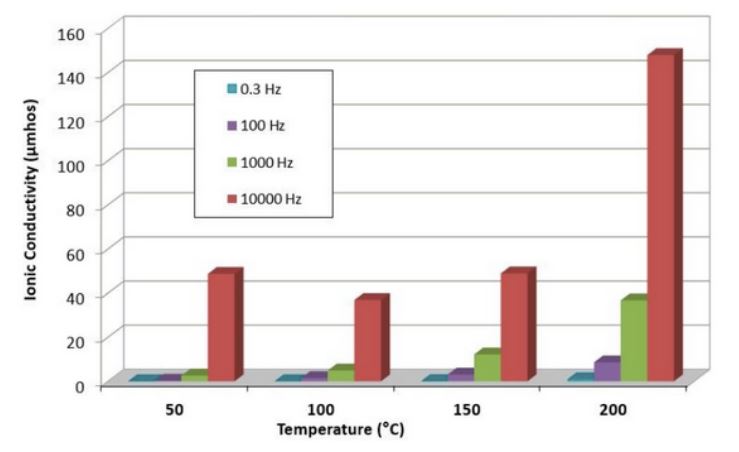