Although it is just a small detail, tightening screws plays a crucial role and needs to be given attention. Simple mistakes, such as over-tightening or under-tightening screws, can lead to serious consequences, from equipment malfunctions to hazards for the user. Particularly in applications that experience high vibrations, improper tightening can result in loose joints, causing unexpected failures. This article will highlight some disadvantages of traditional screw tightening methods and introduce threadlockers technology.
Disadvantages of traditional screw tightening methods
Currently, many manufacturers are still using mechanical screw tightening methods such as spring washers or nuts and bolts. However, this method has some limitations, including:
-
Loose screws due to vibrations, temperature changes, or incorrect torque applied to the bolts or nuts.
-
Mechanical devices like spring washers may become compressed over time, leading to reduced tightening force and causing screws to loosen.
-
They do not provide sealing for nuts, especially in locations with oil gaps.
-
Each component must use a different type of washer or nut, leading to storage issues or the need to purchase items individually.
-
Prone to damage due to rust.
Screw tightening solution with threadlockers
The limitations of traditional methods have led to the development of threadlockers (or screw tightening adhesives). This type of adhesive makes the screw tightening process easier, eliminating issues that hinder the durability of joints against impacts, dust, oil, chemicals, and more, with clear benefits such as:
-
Tightening nuts onto bolts before the effects of vibrations and temperature changes.
-
Sealing the interface between the screw thread and the nut to prevent fluid leakage from inside or rust caused by external chemicals.
-
Suitable for use with any type of screw, regardless of shape or size.
-
In many cases, screw tightening adhesives are also used as lubricants during the tightening process.
How to choose suitable threadlockers?
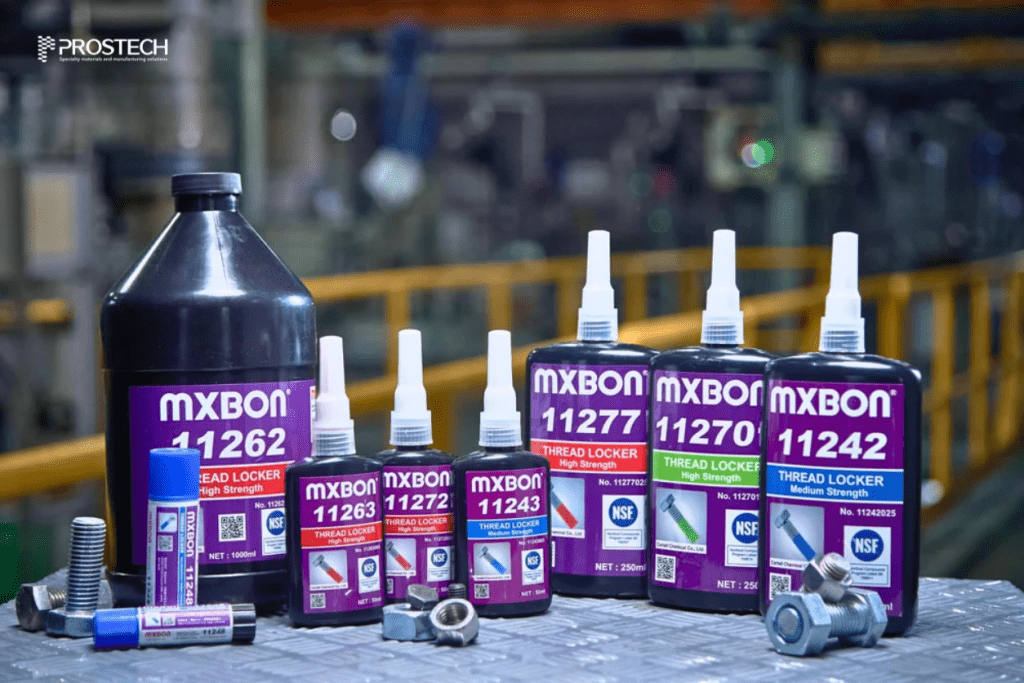
Today, there are countless types of threadlocker available in the market that cater to various needs. Here are some factors to consider to help you choose the right threadlocker.
1. Force and torque required for tightening
Threadlockers are often distinguished by color, such as purple, blue, red, and green. The color of the locking adhesive is typically used to differentiate the locking strength and their applications. Each color represents a different level of tightness, ranging from easy removal to extremely secure. This helps users easily select the appropriate type of adhesive for their needs.
-
For Low Force Usage: Purple threadlocker is suitable for bolts and nuts with a diameter of approximately 6mm, which can be easily disassembled using handheld tools like wrenches or torque wrenches. This type of threadlocker is ideal for joints that need to be frequently disassembled.
-
For Medium Force Usage: Blue threadlocker is the most widely used type because it is suitable for a variety of applications, especially with bolts and nuts ranging from ¼” to ¾”. Additionally, this type of threadlocker allows users to easily disassemble connections using just handheld tools.
-
For Medium to Strong Force Usage: Green threadlocker is designed to provide the best tightening and adhesion for bolts or nuts from ¼” to ¾” (6mm to 22mm). To remove this type of threadlocker, high temperatures of up to >550°F/260°C may be required, followed by using handheld tools to loosen the nuts while still hot.
-
For Strong Force Usage: Red threadlocker creates ultra-secure, almost permanent connections, typically used for joints that never need to be disassembled.
2. Viscosity of the adhesive
-
Completely Liquid Adhesive: This type of adhesive is very flexible, easily penetrating small gaps, and is suitable for applications requiring high precision. Therefore, it is widely used in many applications, especially for bolts and nuts with small thread pitches or threadlocking for sealed threads.
-
Medium Viscosity Adhesive: This type of adhesive strikes a balance between flowability and adhesion, is cost-effective, and is suitable for overhead applications and vertical surfaces.
-
Threadlocker Tape: Can be used in applications requiring pre-application on bolts and nuts several days before tightening the threads.
3. Timing of threadlockers application
-
Use Before Thread Tightening: Threadlocker tape is the optimal choice in this case. Additionally, some liquid adhesives can be used, but it is essential to ensure that the surface drying time is sufficient so that the adhesive does not run during tightening.
-
Use Concurrently with Assembly: Most types of threadlockers can be used in this scenario, as the adhesive will be applied to the bolts and nuts while assembling these two components together.
-
Use After Assembly: Green threadlocker (wicking grade) is the appropriate choice because it can deeply penetrate small gaps, enhancing the durability of the joint.
4. Application substrates of threadlockers
-
Metal to Metal: This is the most common application for threadlockers.
-
Plastic to Plastic or Plastic to Metal: It is essential to choose a specialized adhesive to ensure good adhesion and to avoid damaging the plastic surface.
Some popular threadlocker products
![]() |
![]() |
![]() |
Blue Threadlocker MXLOC 11242 | PERMABOND® A130 Anaerobic Threadlocker | Threadlocker PERMABOND HH131 High Temperature |

The choice of the appropriate threadlockers depends on the specific requirements of the application and environmental conditions. Each type of adhesives offers its own advantages and is suited to different demands during the manufacturing and usage processes. With many years of experience in the industrial material, Prostech is ready to assist customers in selecting the right potting compound and providing integrated solutions for production lines to optimize manufacturing efficiency. Contact us for free consultation.