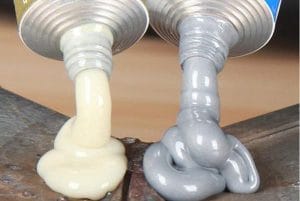
On the journey to analyze your adhesive option, high chance you will come across the controversial debate between 1K and 2K adhesives. The most correct answer would be neutral since each type has its own pros and cons, which make them suitable for different kinds of applications and industries.
However, if you are still confused on which option works best for your application, we are here to help. This article will go through the most significant aspects of 1K and 2K adhesives and compare to see how different they are under the same circumstances.
1K and 2K Adhesives – What are they?
- 1K adhesives are said to have only one component. In fact, they have two components (“resin” and “hardener”) but they have been mixed by manufacturers and are always in ready mode to be used as a single unit.. These adhesives require an external factor (like moisture or heat) to start the curing process.
- Meanwhile, 2K adhesives contain two components – “resin” and “hardener”. These are two completely separated components which will be mixed with specific ratio before usages. When these components are mixed, there will be a chemical reaction initiating the curing process.
The mixing ratios are varied: 1:1, 2:1, 4:1 or 10:1 are all acceptable based on types of adhesives and their formulars. These different ratios lead to flexible versatility, which will be discussed more in our second part.
DO NOT MISS How 2K Meter-mixing and Dispensing System work
1K and 2K Adhesive – Comparison
Now it’s time to answer our main question: the differentiations of 1K and 2K adhesives and what factors to consider to pick out the right one.
|
1K Adhesives |
2K Adhesives |
Mixing process |
Since there is just one part, there is not much to go wrong. The manufacturer has already taken care of the mixing process. So, typical things you need to pay attention to are product suitability and proper application. |
It is very difficult to assure the application process is done right every time. Even when you use the right ratio, there are still the risk of air bubbles, conductivity, or improper mixing. Hence, the adhesive cannot form a sufficient bond which lead to adhesive failure. Unfortunately, there’s nothing you can do once the mixing fails but to remix a new one. |
Dispensing technique & levels of human resources |
As a result from the mixing point, dispensing technique of 1K does not require high level of skill from the operators. Quality check frequency can also be reduced since there is less to worry about. |
As the issue mentioned with the mixing process, the biggest risk is to mix the components incorrectly. To reduce that risk, the operators need to be trained properly. Also, the process needs to be followed in order to ensure the adhesive quality. |
Curing time & condition
|
1K adhesives have specific requirements to cure: moisture and temperature. If the curing condition is not sufficient, the adhesive will not cure effectively. |
Different to 1K, 2Ks don’t rely on external conditions (such as temperature and moisture) to initiate the curing process. The hardener part will start the curing process and will guarantee it cures the whole way through the adhesive. |
Versatility |
1Ks don’t give you numerous options with tweaking characteristics (such as strength or speed of cure). This is because there is only one part to be adjusted. |
Since 2Ks allow you to adjust the formulation, you can tweak the adhesive to follow your characteristic requirement. For example, you can set the adhesive to have a very specific open time before curing very quickly. |
Cost |
Compared to 2K adhesives, 1Ks definitely cost you less. There is no special requirement for equipment or packaging, which also causes less wastage. Moreover, labor cost can be saved since the requirements for skills and degree is less complicated. |
2K adhesives will cost you more. Why? Because specialist equipment to apply 2Ks will cost more. The packaging as 2Ks require also costs more. That’s not to mention the training cost for your operators and QA team. |
Bonding strength |
Bonding strength is probaly the most concerned issue when manufacturers compare between 1K and 2K adhesives. However, there isn’t a specific answer. Bonding strength will depend on chemical base of adhesives. For instance, epoxy-based 1K adhesives can achieve extraordinary strengths and bond better than 2Ks, but PU-based 2K adhesives are stronger than PU-based 1Ks. |
Windup
So there is no superior adhesives for every application – each type has its own pros can cons. In order to choose a type that suits your application the most, put their characteristics in your actual situation to compare. Our advise is, if your applications do not require special characteristic adjustments, 1Ks will be a better option as there are too much that can go wrong with 2Ks. However, it is necessary to evaluate the application comprehensively to choose a best fit solultion.
Need more consultants to choose the right structural adhesives for your application, contact us: